With closed borders and the resultant fall in demand for Australian fresh produce normally destined for overseas Asian markets now is the time to look at how our national supply chain can be repurposed to address the disruption.
The supply chain is a business-to-business story (B2B) starting on the farm, or in the sea, with produce freighted into markets and food outlets. The last mile is a business-to-consumer story (B2C), right into people’s homes using e-commerce/last mile delivery platforms.
In response to the COVID-19 crisis, we’re seeing vital supply chain work being done with partners like Foodbank, and the utilisation of government care packages. But there’s also the opportunity for businesses to rethink domestic delivery capacity. Fleets of vehicles currently delivering supply of fresh products such as bread for four hours each morning, could have their capacity reutilised in other key parts of the supply chain. We could think of this as the ‘uberisation’ of transport and logistics.
Right now, the market wants fresh fruit and vegetables, seafoods and proteins. Yet at the same time there’s a slowdown of transport as domestic borders limit speed of delivery and the return of assets like trucks and containers. There is also the rising cost of freight. Exports are experiencing limited access to airfreight (and even shipping containers) for fresh produce and excessive prices from <$1k up to as high as $25/kg. These prices don’t realistically support exports into Asian markets.
On the domestic front, the high demand surge for B2B-filling of retailer’s shelves and B2C-home deliveries for food, sporting and entertainment equipment is changing transport patterns rapidly. That means pivoting and repurposing transport fleets at the same time building in management of the vital aspects of OH&S and regulatory for food handling and dangerous goods.
What is the specific solution for the domestic supply chain right now?
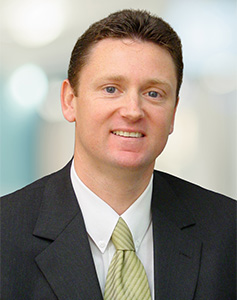
We need to analyse current failures and choke points driven by the COVID-19 pandemic and build new business continuity planning models. The aim is to put supply chain front and centre in reshaping activities. In other words, identify by critical industry what must change to support Australia as a self-sustaining country.
Whilst certain businesses can defer activity like fishing for lobster and other seafoods, other commodities like fruit and vegetables must be harvested or they go to waste. For these commodities, it is time to pivot and re-purpose – moving fresh into frozen products, extracting key properties as inputs into vitamins and supplements or as ingredients into food and beverage manufacturing. These are just a few examples of how businesses must think differently during times when borders and access to traditional markets remain closed.
Additionally, we can also look at the flow of inbound and outbound products through the lens of regional and local supply chain flows. Wherever possible we must seek to utilise alternative modes of transportation and conduct trade-offs according to criticality, needs, cost, service, and risk scenario analysis of all viable options.
How can we understand ‘criticality’? The answer is firstly on type (fresh, perishable) and then supply criticality. We need to create inventory and supply visibility across the end-to-end chain – identifying those critical choke points and reconfiguring flows, storage, and domestic supply chain structures.
Supply risk management is based on four key factors: item classification; supplier location (local, interstate, offshore); alternate supply options, alternatives; available transport routes and lead-times (potential delays across state lines, access to road and rail freight, access to food containers).
Pivoting and repurposing also involves mapping the supply chain. That is about enabling better visibility of several tiers of suppliers, as well as the logistics between those suppliers. We need to know where the alternative routes and access points are to be ready when disruption (eg. no freight or container access) hits the supply chain.
Businesses need to conduct a value chain assessment of other risk factors that may escalate costs. This includes knowing that transportation shortages may increase cost (as transport companies see an opportunity to raise margins) and impact service and inventory capabilities. It’s essential to take proactive action to address anticipated shortages, such as possibly pre-booking/consolidating freight for charters with others – even competitors! Another intelligent approach is to identify additional supply sources even across other industries, near-shore options and/or identify collaboration opportunities with competitors in the same geographical area.
By shifting production closer to the end customer, organisations can offer faster fulfillment at a lower cost and with a smaller carbon footprint. Micro supply chains also mitigate the impact of reverse logistics, the annual cost of which in the U.S. alone is expected to reach $550 billion by 2023. Working within rather than across borders means micro supply chains are far less vulnerable to changes in regulation, interest and exchange rates, wage inflation or tariffs. The ability to manufacture in smaller batches keeps inventory costs and waste to a minimum.
Supply chains of the future won’t be driven by products and processes, but by customer needs. They won’t depend on capital-intensive fixed assets and linear flows but on an ecosystem of modular capabilities, delivered through a network of trusted third-parties that can be scaled and recombined as needed. It’s likely too that operators will become managers – and that means new skills will be required and new job roles created. That’s the evolution we’re seeing; pivoting and repurposing now will help us get there.
Peter Liddell is partner, ASPAC head of supply chain for KPMG. This article first appeared on the KPMG newsroom website. Reproduced with permission.