The Swiss Bell Food Group is in the middle of its digital transformation. Its CIO Sven Friedli emphasises two pillars: a reliable IT partner, like the ERP provider CSB-System, and the right technologies to achieve the business goals.
“Our Spanish ham factories are a good example for the benefits of digital solutions. With a turnover of 15 million kilograms per year, you always need up-to-date inventory information, optimum production, transparent warehouse management, and secure traceability. For this, digital technologies are imperative,” Friedli says.
Since October 2020, Friedli has been chief information officer (CIO) of Bell Food Group based in Switzerland. He graduated in information management and business administration, so he sees the IT decisions in the day-to-day business from a broad entrepreneurial perspective.
He says digitalisation measures should always solve a specific problem in the company, and they should have a positive effect on the quality of data, the costs, or the sales. “With digitalisation, we aim to enhance the fulfillment of our business requirements and to work profitably in the entire group,” he says.
Looking at the technologies behind this strategy, you will recognise most of the components: ERP; MES; supply chain solutions; data terminals in the internal goods flow; and robotics ensure the envisaged integration of business and IT. Software modules like production planning or cutting planning are used to improve the transparency and to achieve efficiency gains at different locations.
Founded by Samuel Bell in Switzerland in 1869, the former small-scale meat processing company evolved into an international player with activities in 15 European countries, from Spain to Romania.
“Our product lines include meat and poultry products as well as charcuterie and seafood. We are also active in the convenience sector, so we produce everything from salads and sandwiches to ready-to-eat pasta dishes, soups, and more,” reports Friedli.
“We employ around 12,000 people at our 63 facilities, and we have a huge network of suppliers and sales partners in the food industry as well as in the IT sector who help us to meet the demands of our customers.”
IT partner as an important pillar in the digital transformation
One aspect that is often underrated in the digital transformation is the significance of a functioning partnership between the user and the ERP provider. There are many examples showing that good tools are just one important pillar for the success of transformation processes.
Another, at least equally important, pillar are the people. The Bell Food Group successfully cooperates with the ERP industry specialist CSB-System. “From among our digitalisation projects, the ERP projects at our Spanish facilities have especially excelled with a high implementation quality.
“The collaboration between all parties involved ran like clockwork, everyone spoke the same language, and they all worked towards common goals. But this is not necessarily guaranteed.”
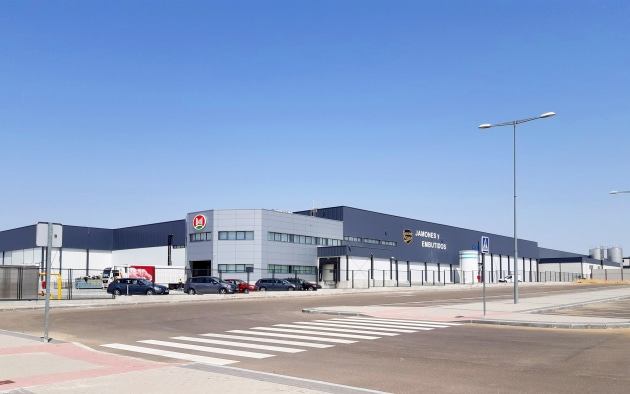
Decision-makers in the food industry only know too well from their own experience what Friedli is talking about: value-adding processes and complex IT and OT structures that have grown over years cannot be transformed at the press of a button.
Implementing a software system for HR or accounting is one thing. But digitalising factory processes and optimising the shop-floor management is something entirely different.
These undertakings are change management rather than mere technology projects.
Besides a suitable Factory ERP as the central nervous system, the consultants play a crucial role as they know the software and the business requirements. For this, you need a deeply rooted understanding of the needs and challenges of the food industry.
Genuine cooperation between the ERP provider and your own staff, in local conditions, are essential to design optimal processes.
Friedli therefore expects the IT consultants from their IT vendors to be at home in two worlds: in IT, and in food processing. “We are all in the same boat. It is therefore important to have a common understanding of the processes in food production. A mere IT specialist without extensive industry expertise could do little to help move us forward.
“Peter Ettrich, head of the DevOps Centre, speaks highly of CSB and the entire CSB project team. They have brought the digitalisation at our ham factories to a new level.”
Spanish ham factories reach new efficiency levels
In fact, the ham production facilities in the Spanish ham regions Extremadura and Castile-La Mancha have been brought to an entirely new efficiency level over the past few months.
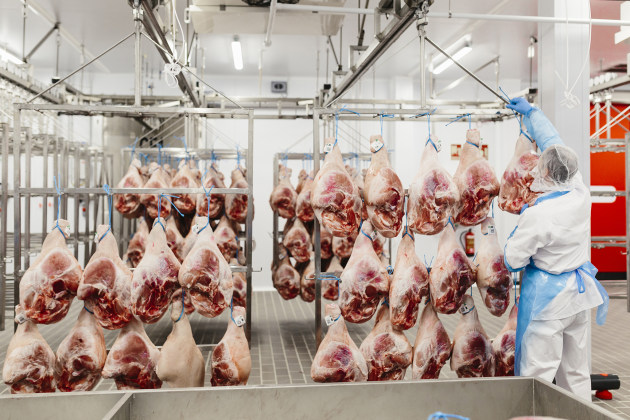
Until recently, redundant work steps and incomplete information were substantial cost drivers. One of the most important requirements of the Bell Food Group was the change from a paper-based data capture and execution to a digital information flow, for example in the processing of receipts, purchase orders, and traceability.
On an area of 65,000 square metres, with 120 full-time employees, and a production capacity of 5000 tons of raw ham (including the popular Jamon Ibérico), Bell’s factory, located south-west of Madrid, is one of the most important production facilities for the company’s raw ham sales in Europe.
“It is a delicious and expensive product that is produced on a large scale,” Friedli says. “We are talking about up to one million hams hanging in our warehouses in Fuensalida for drying and aging.”
With different breeds of pigs that are processed in different types of ham, with different curing and aging times depending on the quality and the designated certification, maintaining traditional methods dating back over a thousand years on a large scale, and in an industrial environment can be challenging.
“In the past, the facility did not really have an exact, comprehensive overview of the production process,” explains Friedli. “For stocktaking, for example, it took weeks to count all hams. Now, we have introduced an integrated supply chain solution that tracks the entire process, from the purchasing of the pigs up to the sale of the ham. All information and data is available in a single system across the entire process so that stocktaking is accomplished with a mouse-click, just like checking the revenues.”
“The quick availability of information in the ERP enables us to act much quicker,” explains Peter Ettrich. He is responsible for the CSB applications at 19 Bell factories all over Europe, and he was the overall project manager for the project in Spain.
Also in labelling, the company saw rapid progress thanks to the reduction of errors. The installation of a ham grading system has advanced the integration of software and hardware.
In addition to that, ERP has generated added value by optimising order picking. While pickers in the food sector often spend more time on running, searching, and printing than on the actual picking process, the Bell Food Group again counts on digital information instead of paper forms. The use of hand-held devices not only accelerates the process, but also reduces errors and additional work.
The project was a huge success and has helped Bell Spain overcome problems in the production processes by means of technology. Friedli says it was an achievement only possible because the IT team and the consultants at Bell Spain devoted a lot of time to understand the problems and how technology could solve them.
“We intensively investigated the steps in production, the type of reports required by the company, and the best ways for generating useful data from the various steps of the production cycle.”
Jointly implement realistic use cases
Digitalisation is nothing new for the Bell Food Group. It has been underway in many parts of the company over the last 20 years. Office work processes, batch processing, picking, inventory management and machines have been at least partly digitalised.
In 2005, in Oensingen, Switzerland, a high-bay storage facility controlled by RFID was put into operation, pioneering state of the art operations in the meat industry.
Now, the goal is to link single digital islands in an integrated network. For example, getting a better idea of the big picture by incorporating recent acquisitions into the information technology to obtain global data.
Austrian poultry specialist Hubers has become part of the corporate structure just like Eisberg AG in Switzerland and Süddeutsche Truthahn AG from Germany. Bringing new facilities on board always entails the question how to accommodate their IT: how can the integration succeed despite heterogeneous maturity levels of the different sites?
There is still a great deal to be done. “We are aiming for operational excellence,” says Friedli referring to the upcoming projects they want to deliver with the CSB team at various locations in Europe. One example for the next level of productivity is the Manufacturing Execution System for cutting at a facility in Switzerland, also provided by CSB.
The group’s goal is to further enhance data-driven decision making to ensure its success. The direct costing and marginal costing system – currently in its pilot phase – is intended to bridge the gap between shop floor and top floor.
Ultimately, this is about continuous improvement of processes and initiating new digitalisation activities with the ERP. The goal is a digital end-to-end chain from forecasting to scheduling and shipment, incorporating quality assurance as well as cutting, packing, and logistics.
Leaving the urge for optimisation aside, Ettrich and Friedli agree that, “it is important to know the needs of the business units and to consistently pursue them taking an iterative approach. You only achieve the right goals if the digitalisation presents a clear benefit for your business.”
This is a sponsored post supplied by CSB-Systems. For further CSB-System case studies visit the website, YouTube, or LinkedIn.