Victorian-based Enmin Vibratory Equipment has moved to much larger facilities as well as expanding its areas of expertise. The custom vibratory and material handling solutions company has been operating for more than 40 years, with its new location in Braeside.
The move give’s Enmin three times the space of its previous location, allowing Enmin to increase its production capacity, bring more of the manufacturing process in-house and offer a broader range of support services.
Enmin general manager Anthony Gallaher said the move would allow the company to take even more control of a project from initial sale and design through to fabrication, assembly and testing.
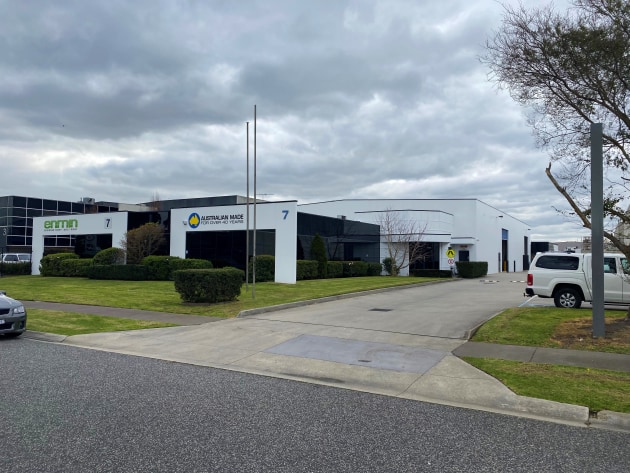
“The changing global environment has highlighted more than ever the necessity to be in control of all aspects to ensure supply can equal demand,” Gallaher said.
The new facility is 2642 square metres, with 1380 square metres allocated to a split factory space. Factory A is used for assembly, parts storage, equipment testing and system assembly, whilst Factory B is used for manufacturing, fabrication and customer acceptance testing.
“Our vastly expanded factory area will see customers benefit from our ability to stock a larger range of standard parts allowing them to replace on demand; being a local manufacturer means no waiting for parts from overseas. We are only a quick phone call away to immediately respond to any customer query or provide service throughout Australia,” Gallaher said.
New speciality services added
The move coincides with Enmin expanding into new areas of expertise. This includes project management, covering planning and SAT-Site acceptance testing, equipment installation and on-going equipment maintenance.
A separate division has also been created for Controls & Automation, capitalising on Enmin’s extensive experience in providing electrical control and automation services for the food and allied industries.
“We carefully review a customer’s automation requirements and then tailor a solution to best match their specification and budget.
“Systems are designed with future requirements in mind to provide flexible and expandable plants. As well as new build equipment, we can seamlessly integrate controls and automation into new or existing production lines,” Gallaher said.
Enmin has also been busy working on new product development. The company has recently designed a new range of ‘off the shelf’ modular systems for seasoning, sprinkling, packaging and an in-line blending system. These products can be purchased individually or integrated into an existing or new materials handling system.
Industry commitment
Gallaher said: “One of the outcomes of the COVID pandemic is the recognition of the importance of nurturing and assisting local manufacturing. This is reflected in the support that the Government is providing Australian manufacturers to encourage greater investment.
“We’re very proud to have been an Australian manufacturer for over 40 years and see many benefits in remaining so. Our customers benefit from our ability to offer individual design and customisation whilst enjoying expert local advice, guarantee of supply and outstanding back-up and support. We also continue to support other local specialised manufacturers,” Mr Gallaher added.
The company has also employed its first apprentice in the welding and fabrication area. “We recognise the importance and necessity of companies putting on apprentices in a growing Australian economy where skills and knowledge are paramount - we’re extremely proud to be doing our part,” Mr Gallaher said.
“The move to larger premises and all the associated benefits it provides us and our customers is a very exciting time for the business. It demonstrates our commitment to designing and building the finest materials handling equipment made right here in Australia. It represents the next stage in Enmin’s history, or as I like to put it, Enmin 2.0,” Mr Gallaher concluded.