As one of the world’s largest manufacturers of industrial processing, conveying, weighing, packaging and inspection systems, Heat and Control is at the forefront on adopting and adapting Industry 4.0 changes. This article first appeared in the July 2021 issue of Food and Drink Business.
Q How is Heat and Control equipment adapting to Industry 4.0?
Most of our equipment has programmable controllers that allow connection to plant MES or data acquisition systems and can be remotely accessed for commissioning and customer support. The continued evolvement of machine and device level networks means more data is available, as well as providing the end user with the capability to store, recover and analyse the accumulated data.
Q What are the main benefits of data integration and process monitoring?
Industry 4.0 has seen a renewed focus on innovation and is transforming how the food industry operates.
Intelligent factories are seeking to optimise their processes to adopt lean manufacturing principles.
Heat and Control has long held the philosophy of continuously improving our machine designs through ongoing R&D investment, so that we can provide customers with solutions to improve their operations through automation and efficiency.
Every processor wants to identify and classify hidden issues in their production flow before a problem arises. Data integration and process monitoring are beneficial by facilitating the collection and retention of important production data and creating a database of vital information on the production run.
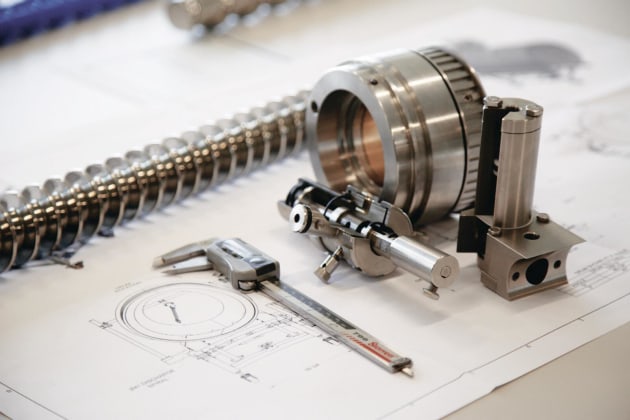
As a single source supplier, we add value through increased connectivity levels and digital data exchange, at all stages of the processing and packaging production line. For example, integrated product handling and processing lines for potato processors benefit from custom made fryers, heat exchangers and oil filtration systems, which integrate with our FastBack Conveyors to deliver product at twice the rate of comparable conveyors for high-speed production.
Q Staying with potato processing, what’s the “next big thing” for the industry?
Innovation in processing equipment is seeing certain elements of the production line streamlined or eliminated altogether, while process monitoring, and data integration will continue to evolve at a rapid pace.
Understanding the importance of frying during the processing stage, and ways to automate and simplify frying control have long been a priority.
Heat and Control fryers have automation control which uses feedback from a moisture meter after the fryer, to control frying temperature and dwell time to meet moisture targets. This improves the quality of the final product, increases the shelf life, and ensures the product is the right size, shape and texture.
The frying parameters can be monitored remotely, giving the operator flexibility in how they manage the fryer. Waste can be monitored at key gateposts in the production line by using product weighing systems to control throughput to optimise the whole-of-line performance.
Some heat exchangers can be fitted with O2 sensing to automatically regulate combustion levels to save fuel and reduce emissions while ensuring continuous efficiency.
With more competition than ever in the food processing industry, especially snack, traditional manufacturing methods will continue to make way for innovation and lean manufacture.
Q How did Industry 4.0 help you during COVID-19?
The pandemic has driven us to proactively address the changing marketplace in terms of supporting our customers while minimising risk to them and our employees.
Technologies such as MS Teams and Zoom have helped us to maintain customer contact, support operations, field service, spare parts shipments, and ensure our manufacturing capability.
Customer camera options such as GoPro for both pre-delivery inspections and site visits have been used to assist with social distancing and gaining virtual site access during times of restricted travel.
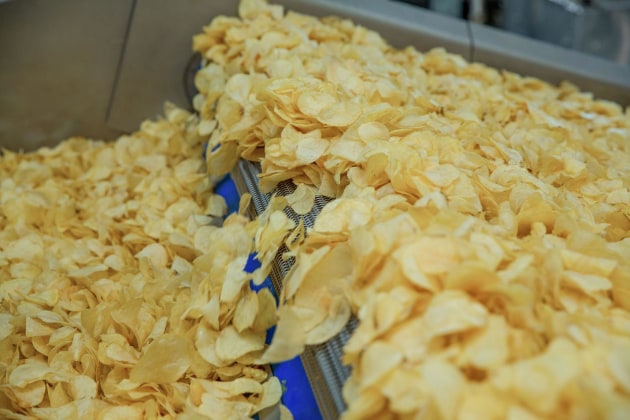
In close partnership with our customers, we have expedited our development of remote testing, sales, training and service capabilities, which have allowed us to meet our customers new product/project needs while supporting the tens of thousands of machines we have installed around the globe.
Q What has been the biggest challenge in designing and producing processing equipment that has the capability of hardware and software integration?
Over the past five years, the integration and networking space has evolved rapidly and continues to do so.
One of the bggest challenges is keeping up with trends and the speed at which new equipment and systems become out of date or obsolete.
You must keep up as there is potential to lose scalability and networking capabilities which newer systems include as standard. This then flows on to the end user’s ability to integrate the equipment into their plant systems.
We have found that by keeping up with technology, devices are more easily integrated into a control system and by taking advantage of this we are able to reduce engineering and provide access to more data.