In this new content series, Food & Drink Business takes a closer look at the opportunities inherent in the fast-evolving food processing industry, with insights from leaders at companies which have signed up to exhibit at APPEX 24.
This month we speak to Robert Marguccio, Packaging & Inspection Systems business manager for Heat and Control.
The Australian manufacturing sector is at a critical juncture as it seeks to grow onshore capacity and capability while remaining globally competitive. With reference to your business, what do you see as a) the key challenges and b) the main growth opportunities inherent to this dynamic sector?
There’s no denying the industry is in a state of transformation. As global demand for convenience foods, ready meals, packaged snacks, and frozen foods continues to rise, food processors are also dealing with rising cost of energy, resources, labour shortages and raw materials.
To meet these challenges – processors will need to find innovative ways to be profitable, remain competitive, and unlock growth during these turbulent times.
A focus on greater production efficiency, resource management and sustainability will be critical, and each of these areas has the potential for optimisation with the help of technology and automation.
And, while improving each of these areas individually can be highly beneficial – and addressing all of them together, with an integrated approach – is an excellent strategy to future-proof your business.
What role has automation played in growing your business and advancing your customers production performance?
At Heat and Control, we have well-developed solutions for almost every application. We’ve been setting benchmarks in industrial food processing for over 70 years; advancing our customers production performance so they can offer their customers the very best products – is why we exist.
We help our customers choose the right equipment and technology for their application, to achieve the most optimal setup to improve production performance. No two installations are the same, and automation will mean different things for different organisations.
It could be achieved with a single piece of equipment, or an entire line; but regardless of the scale, our solutions automate by incorporating the various processes, resources, and systems within the organisation.
Our process expertise is what sets us apart as a business, and we’re passionate about helping our customers understand all the available options (for their specific application) and explaining the technology in plain and simple terms.
What innovative technology/product/solution has your company brought to market recently that sets you apart from your competitors?
Investing in innovation is at the heart of what we do here at Heat and Control. Our solutions are designed in-house, or as a result of collaboration with brand partners, for instance Ishida or CEIA. One example of an innovative solution we’ve introduced recently, with partners Ceia, is a self-testing and calibrating metal detection solution for snacks processors.
Using a metal detector is a quality control requirement, but this solution can remove the need for hourly manual testing of the operational limits of the unit. It does so by using a test signal – instead of an externally introduced test piece – and is done on the fly and logged as a pass – so the line doesn’t stop. This innovation saves around 10 minutes per hour in testing, as validation takes relatively no time. And, when there is a problem, it stops the line and alerts the operator.
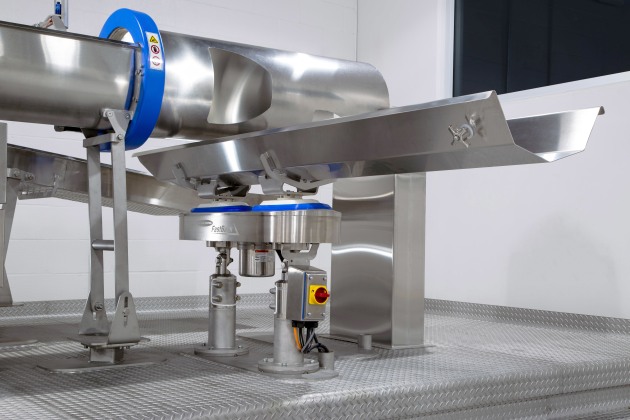
When we design equipment – high performance equipment, that delivers results is our top priority. Our FastBack range of conveyors are recognised as the number one brand in horizontal motion conveying, but last year we introduced a completely new solution for this category.
FastBack 4.0 – is a circular to linear drive horizontal motion conveyor that offers unprecedented performance to food processors. A key feature of this new solution is a new drive mechanism – which uses rotational (circular) drive motion to produce a horizontal (linear) motion.
It’s a truly innovative design that uses circular-to-linear drive efficiency – to convert rotational motion into pure horizontal motion – while also supporting the vertical weight of the pan. This patented circular motion can gently handle product – so it’s undamaged and the coatings are undisturbed – while also achieving industry’s highest travel rates, and flow rate capacity.
This equipment is the culmination of more than 10 years of development, multiple international patents, and a development partnership with industry-leading industrial bearing manufacturer SKF (AB SKF).
Working with your customers, what key trends are you observing unfold in the Australasian food and beverage processing sector?
Efficiency, resource management and sustainability are trending topics, across the board. High performing, energy efficient food processing equipment has long been our focus – and the challenging market conditions we’re currently experiencing is seeing many customers seeking to either adapt, upgrade or investigate – ways to optimise their operations. Equipment and technologies to reduce fuel costs, energy waste, air pollution, and water consumption are key talking points.
APPEX is a new, all-encompassing trade show for the processing and packaging industry. Your company has signed up as an exhibitor at the inaugural show in March 2024, what made it a compelling platform for your business?
As one of the founding members of the original APPMA – Heat and Control have been exhibiting solutions for the Australian packaging industry since 1987. We’ve been part of Auspack since its inception and during this time we’ve seen the food processing industry grow exponentially. Bringing everyone together to have one show for the entire industry makes a lot of sense. And, as a supplier of both packaging and processing solutions, it suits us perfectly, and we’re excited to see what APPEX delivers.