According to its dictionary definition, a warehouse is ‘a large building where raw materials or manufactured goods may be stored prior to their distribution for sale’.
This is of course an accurate physical description of the building. However, in today’s world of just-in-time deliveries and often complex and extended supply chains, the role of the warehouse is increasingly dynamic and significant in the fulfilment of orders with very short lead times.
The realities of daily production mean that it will not always be equally matched with sales volumes and, particularly where demand can fluctuate, order lead times may be shorter than manufacturing time. In factories producing multiple products, supplies of raw materials can vary, which could affect when different lines are able to be produced. And where goods are not delivered immediately after production, they need to be stored efficiently to expedite picking and delivery.
In short, factory warehouses help to buffer production and sales; distribution warehouses facilitate efficient logistics. Combined, they are able to satisfy conflicting demands by enabling efficient production and logistics, together with short lead times.
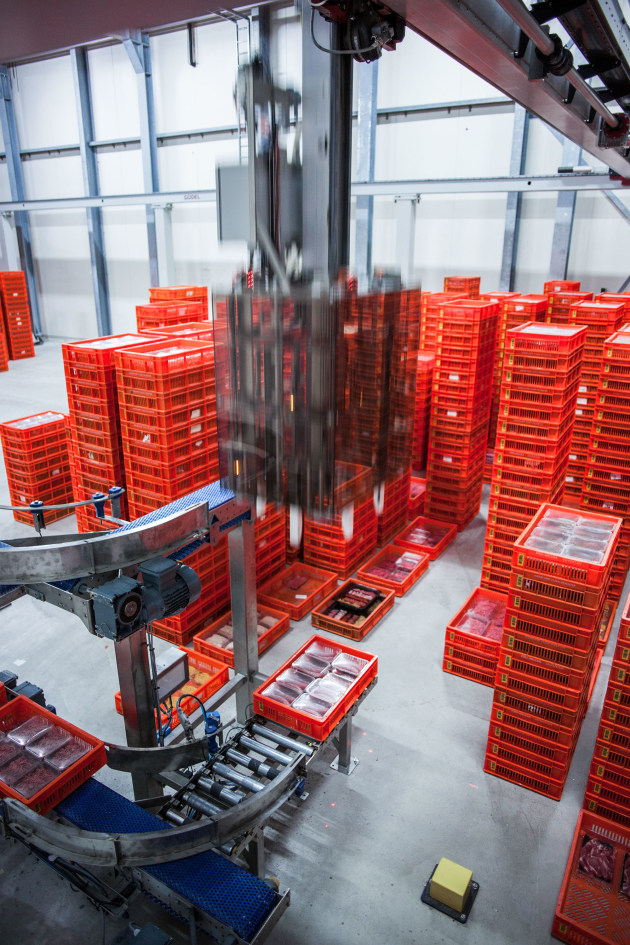
The point is that the physical properties of the warehouse on their own cannot achieve all this. What is required are the joined-up data flows and detailed planning that can be derived from a comprehensive IT system. Through digitalisation, the process that takes raw materials to final products can be effectively managed at every stage, from the receipt and storage of ingredients through production, packing and inventory to storage of finished goods before final delivery.
And at the start and end of the process, with the right IT support, the warehouse’s role is critical. Effective monitoring and control of goods receiving will help to provide ongoing assessment of suppliers. Keeping track of stock on hand avoids any unwanted surplus and maintains quality and freshness, while ensuring goods are re-ordered in good time. This is a particularly vital factor when dealing with food products that have a limited shelf life.
During order fulfilment, the right software and hardware work with warehouse personnel to ensure maximum speed and efficiency. Orders can be processed by scanning on mobile data entry devices; ‘pick to light’ enables direct transmission of incoming orders to displays in the picking area; ‘pick by light’ locates items to be picked by means of light signals; ‘pick by voice’ converts customer order data into speech; ‘pick by vision’ uses smart glasses to enable the picking process; and fully automated sorters or picking robots can be installed for efficient picking of mixed containers.
For companies, this translates into enhanced efficiencies and faster response times. To take a real-life example, at our customer Edeka, one of Germany’s leading meat processors, details of all incoming raw materials, auxiliary supplies and operating materials are posted directly to the company’s ERP system using on line barcode scanners and MDC (mobile data capture) devices. This ensures that no matter how goods are processed, the system knows at any time where to find which goods, thus ensuring efficient material flow in stock placement and removal.
At the end of production, goods are either stored in high bay storage or forwarded to the High Dynamic Storage. The high bay storage facility is automatically managed via inventory management. The software controls all processes for stock entry and removal, the shelf loading devices and the conveyors.
Based on customer orders, the system steers dynamic sorters which deliver ‘goods to man’ or directs pickers up and down the line with lights. These systems ensure excellent ergonomics and deliver high productivity. The process is both error-free and extremely fast, with every employee able to handle up to 700 picks per hour. To confirm the pick process and to provide direct feedback to the ERP system, the operator either uses a touchscreen or push button installed at the workstation, or an MDC device for scanning.
A further benefit of efficient stock management is the ability to enable late-stage customisation as evidenced by another of our meat processing customers Promessa. The company stores sealed, unlabelled products which are packed into cases and registered on the system via barcodes. Fast moving products are stored in the fast mover warehouse in dynamic locations; slower movers are placed into traditional high bay storage. When required, stock is automatically called off and sent to four weigh price labelling (WPL) lines.
In this way, production and storage can be based on forecasts with customer-specific labelling only taking place at the time of picking. This enables optimised batch sizes in production, lower logistics costs, and reduced storage quantities.
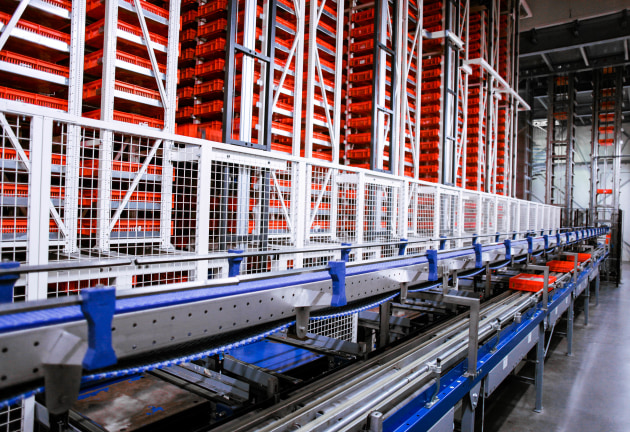
In accordance with FIFO (first in, first out) best practice, our software picks the oldest stock first before sending it up to the WPL lines via automated conveyor. Orders are grouped, labelled and automatically sorted to the pickers by delivery route so that the end result is a mixed case of products for each store to be delivered on a route.
The system allows Promessa to handle even short notice orders, meaning customers can usually receive goods on the same day and the company can also respond quickly to reorders without having to build up large stocks.
Importantly, none of these warehouse operations happen in isolation but are part of a fully integrated process, with software able to monitor, organise and control the entire production process. Such systems provide accurate production scheduling with precise tuning of workflows in terms of time and quantity. Important details, including up-to-date order, production and inventory data, are captured and processed in real time. This high degree of networking facilitates fast and error-free processes and enhanced productivity.
Another benefit of integrating to shop floor machines is the possibility for remote monitoring of equipment which helps to anticipate problems and plan in required maintenance to minimise downtime and maximise Overall Equipment Effectiveness (OEE).
And ultimately, increased efficiencies plus the availability of detailed facts and figures on areas such as gross margins or sales figures per product, customer or country will help to increase performance where it matters most – on the bottom line.
The further advantage of digitisation is that integration is not restricted to within the factory; indeed, the wider the connections across the entire supply chain, the greater the opportunities to improve production and respond quickly to consumer trends and changes in demand.
As a building, the warehouse does exactly what it says in the dictionary. The incorporation of digitalisation, however, adds a whole new dimension to the warehouse’s role in supporting a fast, efficient and cost-effective supply chain.
This is a sponsored post supplied by CSB-System. For further CSB-System case studies visit its website, YouTube, or LinkedIn.