AgriFutures and consultancy RMCG have completed the first ever deep dive into quantifying the scale of waste in Australia's ag sector; from aquaculture and vineyards to orchards and crops, the results may surprise you, but principal consultant from RMCG Anne-Maree Boland looks at scalable and adaptable solutions to make a difference.
While around 70 per cent of the 9.5 million tonnes is organic material that is largely beneficially used on-farm, the reality is that problematic ag waste such as plastic mulch and drip tubes, or timber posts and tyres are stockpiled, burned, buried, or sent to landfill.
Tipping the scales
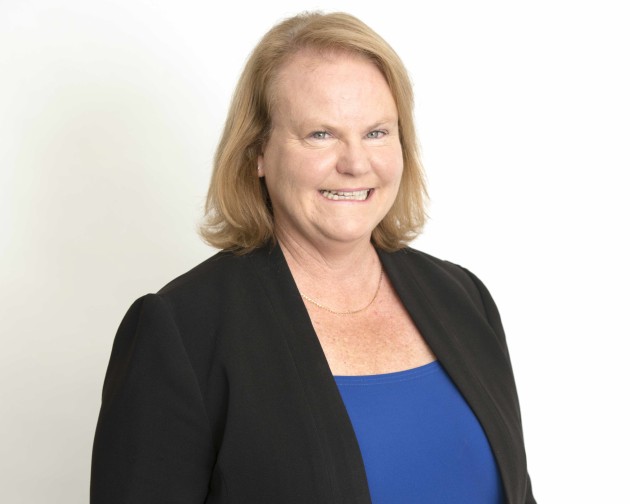
The sector has set its sights on a low waste future, and it has tasked AgriFutures Australia to help. As principal consultant with RMCG, I’ve been working with AgriFutures on the sector’s first ever deep dive into the scale of the problem and the solutions that could change pre-farmgate waste management for the better.
We heard from passionate stakeholders across the ag and waste sectors, including rural Research and Development Corporations, the National Farmers’ Federation, AUSVEG, the Waste Management and Resource Recovery Association of Australia – plus individual farmers and researchers, recycling providers, and regulators.
Uniting them all was a strong commitment to tip the scales for the better.
So, why aren’t we?
By definition, waste is not something people want. For primary producers, that’s especially the case. Abandoned waste accumulates in paddocks, packing sheds and aboard vessels. It’s a messy, sometimes hazardous, reminder of a job not done.
But there are real barriers to pre-farmgate waste management: the cost and time of disposal, the hassle of collecting and transporting waste, and access to reuse and recycling options – especially those that will accept plastics contaminated with organic matter or soil.
To overcome these barriers we need scalable – adoptable – solutions.
60+ innovative ways to curb pre-farmgate waste
Our working group looked closely at 64 innovations that could be investigated – or are being implemented – to reduce pre-farmgate waste. Some are so obvious, you’d wonder why they aren’t commonplace. Like reusing plant pots, or replacing plastic tree guards with compostable ones.
Some solutions punch well above their weight on sustainability. Like creating power from almond waste. Or using seafood shells to regenerate reefs.
But one option could change the game entirely.
Embracing the wonky and wonderful
Around one-fifth of Australia’s fruit and vegetable produce is lost on-farm or in processing/packing sheds every year. Pests and disease play a role, as do seasonal conditions, where bumper crops mean we produce more than retailers can sell. But in a world of filtered photographs and curated Instagram profiles, is it any wonder that the main cause is simply how food looks?
Whole crop purchasing offers an antidote. No more leaving wonky carrots to rot in paddocks; whole crop purchasing involves retailers or wholesalers buying the entire crop – and valorising the produce that’s out-of-spec.
It enables picture perfect produce to be sold to fresh food markets at premium prices, while lower grade produce could go to hospitality and foodservice industries – or as ‘imperfect’ value buys at the supermarket. Any produce unsuitable for these markets could be ‘upcycled’ into value-added products by processing partners.
Such partners already exist, like Nick Stamatiou from Whole – whose proprietary enhanced nutrient extraction technology, WINX, can turn traditionally wasted or spoiled produce into high-value plant-based ingredients that have more nutritional value and are more bioavailable than their original counterparts.
There’s so much to like about Whole’s solution. It’s chemical free, so it doesn’t introduce any ‘new’ waste issues. It creates a high value market for produce that is otherwise discarded. It champions ‘nutrient security.’ It delivers huge capital savings over conventional food processing, because any part of the food product can be processed through the WINX ‘black box.’ And its modular system enables efficient production at scale, solving one of the key challenges facing companies seeking to convert food waste into new products.
With backers including prominent venture capital firms, Artesian and the Grains Research and Development Corporation’s (GRDC) GrainInnovate, Whole. is already turning heads, most recently signing an MOU with one of the world’s largest ingredient companies to jointly commercialise its functional oat product across the world, with additional ingredients like soy, almond, chickpea and lupin also on the cards.
The UK is a few steps ahead of us on the whole crop purchasing journey, with UK food giant, Tesco, already proving that whole crop purchasing can work at scale. In addition to retailing its “Perfectly Imperfect” fruit and veg, Tesco’s ready-made meal brand uses lower grade produce in its convenience meals, where food processing renders only the taste important.
By valuing waste, they’re redefining it, keeping edible food out of landfill, putting more money in farmers’ pockets, and diversifying their markets. If Tesco can do it, why can’t our supermarkets?
They’ve started whetting our appetite for wonky produce – with curly cucumbers, carrots with ‘legs,’ and harlequin capsicums that can’t decide if they’re red or green. But how fantastic would it be to see our supermarkets embrace whole crop purchasing and match the industry’s enthusiasm for innovative, collaborative solutions that cut pre-farmgate waste?
And while they’re at it, deliver a more sustainable, food secure future for tomorrow.
The report, Options for Improved Waste Management, is available from the AgriFutures Australia website.
Anne-Maree Boland is the principal consultant for RMCG.