With 15 key beer brands, brewing giant Lion turned to Dematic to automate its largest facility, the Tooheys Brewery in Lidcombe, New South Wales. This story first appeared in the April 2021 edition of Food & Drink Business.
Lion is one of Australasia’s largest beverage companies, with a diverse portfolio in beer, cider, fine wine, spirits, and both alcoholic and non-alcoholic ready-to-drink beverages. It generates revenue of around $3.9 billion each year.
With a total of 15 key beer brands including Tooheys, XXXX, Hahn, and James Squire, Lion initiated a re-structure of its supply chain and internal fulfilment operations to future-proof its manufacturing and supply chain operations.
Lion’s overarching goal was to make upgrades that would help the company meet the needs of its consumers whilst also looking after its own employees by providing a safe and well-managed workplace.
After significant growth in its product range, the focus was on its largest facility, the Tooheys Brewery in Lidcombe.
The Lidcombe site operates 24 hours a day, seven days a week, and brews roughly 300 million litres of beer per year. It produces up to 120,000 cartons a day, which is equivalent to 2 million litres.
A bigger product range and market dynamics pushing the beverages supply chain into a 24/7 cycle made it clear that Lion’s legacy systems were outdated and in need of upgrading.
Future-Proofing the Supply Chain
As part of the upgrade project, the decision was made to implement Automated Guided Vehicles (AGVs) from intralogistics automation specialist Dematic.
Tooheys packaging manager Tim Symons says the implementation of AGVs was part of a widespread initiative to streamline operations within the Tooheys Brewery and across the entire business.
“We needed a definitive way to improve our productivity to keep up with demand, whilst also remaining cost-effective and competitive within the market.
“We invested in AGV technology as a way to better deliver services to our core assets – our people, brands, production facilities and suppliers – and to generate better value for our customers,” Symons says.
Streamline Operations
Lion selected Dematic as its automation partner due to its track record of implementing automated solutions and its global experience in supply chain optimisation.
The Dematic AGVs were selected because their reliability and consistency eliminated all possible traffic blockages between the automatic palletiser and despatch, even when all palletising lines are running simultaneously.
Symons says its old manual system was less reliable and prone to frequent breakdowns, which would interrupt the entire production facility.
“Also, the reliance on forklift drivers and warehouse worker interactions created a large safety risk. When you combine that with the general inefficiencies of manual forklift operations and the frequent level of maintenance needed to run them, the system was simply not futureproof. Automation was what we needed,” he explains.
A core objective was a solution that would eliminate human contact to products. Using AGVs meant operators no longer had to touch products, lift or transport heavy items and pallets.
“We also wanted the solution to help us optimise our supply chain to prepare it for the future. The reliability of AGVs has given us the confidence that the product we have nurtured through the brewing and production process is going to be a good fit for our customers at the end of the line,” Symons says.
The AGVs increase reliability, are capable of working 24/7, improve efficiency and accuracy of operations, and minimise mistakes, product damage and workplace accidents. All of this leads to significant improvements in occupational health and safety standards.
Dematic general manager of AGV sales Tony Raggio says: “The major requirement for the Lion AGV solution was to operate at a faster rate than any palletisation activity done with a manual forklift, with the end result being to eliminate all manual activity completely.”
At the Lidcombe facility the AGVs work in two distinct areas: zone one and zone two. The zone one AGVs handle full pallets from a robotic palletiser, which has the capacity to handle both twin pallets and single pallets. The AGVs are then brought over to the second zone, where the pallets are handled and moved on to a ‘roll on roll off conveyor’ and automatically loaded into the back of a truck.
AGV management systems controls the AGVs as well as interfaces with a company’s existing warehouse management system (WMS), to track product flow from production to storage and all the way through to despatch. AGVs can also be programmed remotely to carry out required tasks.
“The robust design of our AGVs means it can withstand the typically challenging environment of a warehouse, all whilst providing a 360° safety field of protection with automatic sensors to detect any obstruction. This enables it to co-work with operators and any other warehouse machinery or vehicles,” Raggio says.
The AGV rollout
The AGVs were successfully installed and commissioned while the site was still in full operation, allowing Lion to continue general operations to meet all product delivery commitments during this period. Additionally, Dematic collaborated with Lion to ensure the solution was tailored to, and working effectively within, the facility during this time.
Raggio says: “Through large amounts of coordination, we worked in collaboration with the Lion team and all other on-site partners contributing to implementation of the project. We had our team on-site providing end-to-end management and support to ensure a successful rollout was achieved as quickly as possible.”
Through its full service and support program, Dematic will continue to help Lion on an ongoing basis to optimise system uptime, continuity of throughput and production efficiency.
New solution benefits
For Lion, investing in an advanced automation technology such as AGVs to streamline warehouse operations has been a big achievement, allowing it to gain competitive advantage in domestic and global markets.
“We are very happy with the progress and benefits we have already experienced using the AGVs in the warehouse. It has been an exciting process, and the possibilities are endless with this kind of automation, which has given us a really positive outlook towards how much better operations will run in the future,” says Symons.
The AGV solution has provided Lion with a predictable logistics strategy. This allows Lion to gain insights into the number of vehicles in action within the warehouse, and how many pallets can be produced per day, per shift, and per year – as opposed to a manual forklift environment, which can create unpredictable outcomes such as injuries and staff availability.
Warehouse operators have also experienced significant benefits and better worker satisfaction following deployment of the AGVs, due to the inherent efficiency, productivity, accuracy, quality control and safety benefits that can be gained in comparison to manual goods handling.
Based on the successful implementation of the Dematic AGVs at its Tooheys Brewery, and the operational benefits and improved throughput already achieved, Lion will look to deploy more AGVs at other breweries across Australia.
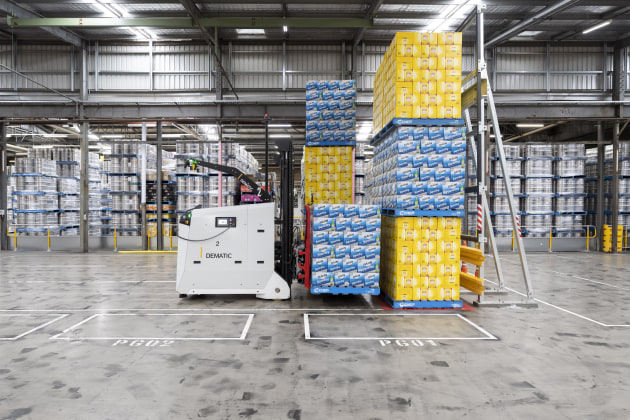
AGV 101
What an AGV is & how it works
AGVs work to manage and automate all activity within the warehouse that would otherwise be operated by manual machinery such as a forklift; working to connect both outbound and inbound products with automated truck loading.
The AGV’s high-precision navigation of the warehouse floor, combined with its dexterous design allows it to utilise any warehouse space, eliminating the need for extensive use of pallet conveyors.
With a smaller turning circle than a forklift truck it can easily manoeuvre in tight spaces.