COVID-19 put new pressures on the food and beverage sector. While the industry is resilient and highly adaptable, the pandemic showed there is room for improvement when it comes to its digital resilience.
“The great enemy of knowledge is not error, but inertness,” British historian Henry Thomas Buckle said back in the 19th century. During a crisis, time seems to move faster, which is no more evident than in the food and beverage sector.
One area that COVID-19 made this particularly apparent was the massive acceleration of interest in tried-and-tested solutions around digitisation. This is certainly good news for the resilience of businesses.
Technology must deliver in difficult situations
Although most companies have managed to get through the crisis, the overall situation is still difficult. The foodservice sector has been particularly hard hit and while the grocery retail industry is in a better position, not all suppliers are financially secure. And the effects are felt around the world. In Germany for example, the Federation of German Food and Drink Industries (BVE) has reported double-digit losses.
Add to this the everyday issues of the food companies: supply chain pressures, labour shortages, the need for production efficiency in competitive markets, and looming price pressure which, according to McKinsey’s recent Disruption and Uncertainty report, is expected to intensify as consumers’ price sensitivity increases.
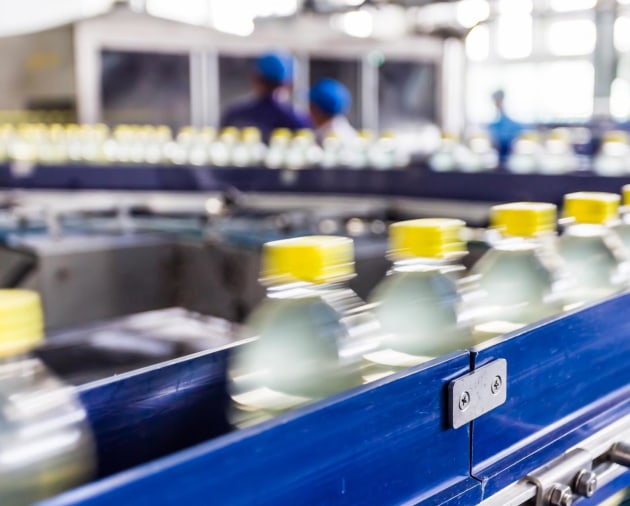
To strengthen the resilience and competitiveness of operations, information technology must ensure three things:
- Flexibility: For food businesses to succeed and prosper, they must be able to cope effectively with both the expected and the unexpected. A high degree of digitally enabled flexibility is called for in the operations as well as in planning and forecasting.
- Efficiency: Especially in just-in-time markets, maximized efficiency is essential – at every stage of the value process. The already small margins should not be eaten up by the inefficiency of shop-floor processes.
- Transparency: An appropriate KPI system ensures that executives can do the right thing, at any time. This could also mean that products with a negative margin are removed from the assortment. Other key issues are product safety and an effective traceability concept.
Use of integrated systems to enhance digital resilience
Results of the CSB survey on the impact of COVID-19 on the food industry show food companies’ digital resilience is better than other sectors. Digitised supply chains are good protection against planning uncertainty or delivery delays. Those who have invested in the integration and digitisation of their value creation processes in recent years can now work better with their partners.
Specifically, businesses with integrated IT and ERP systems are in a good position regarding control and responsiveness of their company. The impact of COVID-19 has highlighted benefits that digitisation brings to companies in terms of virtual collaboration, flexibility and agility of processes, fast and precise planning, and cost reductions.
The survey found that in production and administration, 51 per cent of respondents relied on integrated solutions, while 53 per cent used them for reporting and analytics. However, only one in 20 companies uses intelligent systems.
There are still major opportunities through the integration of market data, especially in regards to changing consumer shopping habits or processes with suppliers, commerce, or customers.
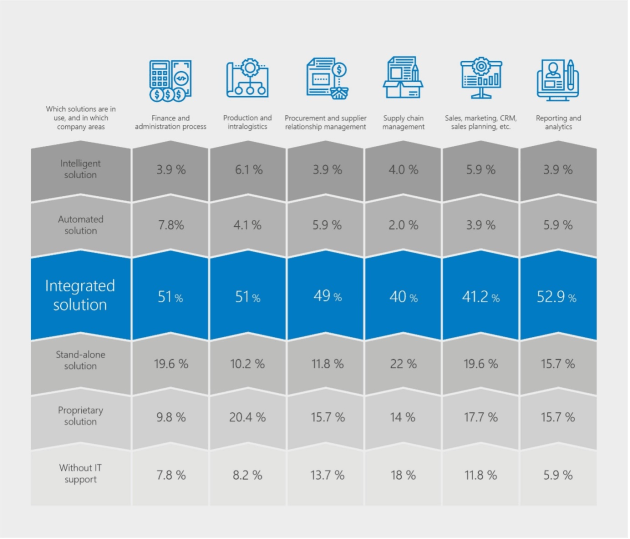
Digitisation is the core competency of food companies
Despite the current achievements of food companies with digitisation, there is no reason to suspend further intensive digitisation. The survey participants agreed that in the future, digitisation would be even more crucial for the economical operation of a factory and for its resilience during a crisis.
Having a firm grip on digital technologies is increasingly becoming a core competency for companies. Indeed, the management of the value-adding processes that take raw materials to final products would be unthinkable without digitisation. From the receipt of goods through production, packing, inventory management to shipment, digitisation helps to make the process as flexible, efficient, and transparent as possible.
The next steps need to be taken now. The goal is to achieve full digital support across the supply chain to utilise further expected benefits for greater efficiency and resilience. The following points reflect the full bandwidth:
Digital monitoring and control of raw materials in goods receiving enable continuous assessment of the vendors, a vital factor when dealing with natural products that do not have a standardized quality.
Effective labelling and identification – using barcodes, RFID chips, sensors, and image recognition – will provide a good overview and ensure seamless documentation. At the same time, this ensures seamless traceability as the data is passed electronically from one processing step to the next.
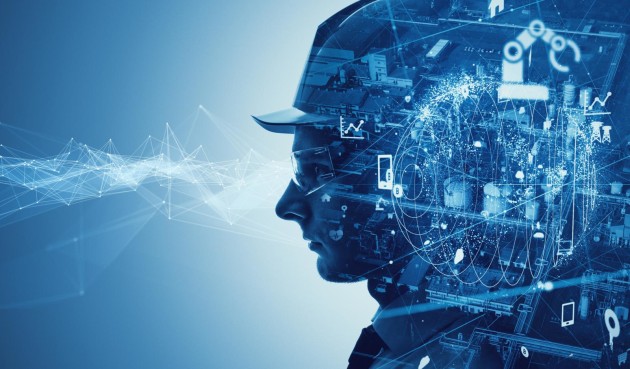
Where the lot sizes in production are decreasing, the number of order changes will increase. This leads to overall higher changeover times, great uncertainty in production and staff planning, and added pressure on the productivity. Software-aided production and forecast planning helps to counteract those challenges.
With the right, precise, and up-to-date measures, executives can monitor the performance, to identify problems, and to intervene systematically in order to further optimise the day-to-day operations. Developing digital twins will further improve the KPI systems.
The digital optimisation of the inventory helps to prevent excess stocks while securing timely replenishment.
Remote monitoring of equipment will help to anticipate problems and plan in required maintenance to minimise downtime and maximize Overall Equipment Effectiveness (OEE).
ERP systems can communicate with the equipment in production or picking. Pick-by-voice and pick-by-vision systems guide the employees to the correct area of the warehouse, where lamps and digits indicate the exact position.
The introduction of automation and robotics also supports the effective interaction of data and goods flows. Many food companies have developed ground-breaking standards in intralogistics, specifically in automated production and packing system, automatic depalletisers, sorters, and high-bay storage facilities for pallets or single crates.
Looking to the future
One thing is clear: available tried and tested digitisation technologies will be introduced quicker than exciting innovations. At the same time, today’s technologies are constantly changing and developing. When companies introduce a new IT system, they also need to focus on the future. Artificial intelligence (AI), the Internet of Things (IoT), big data, and blockchain are all new developments that will have key roles to play in coming years.
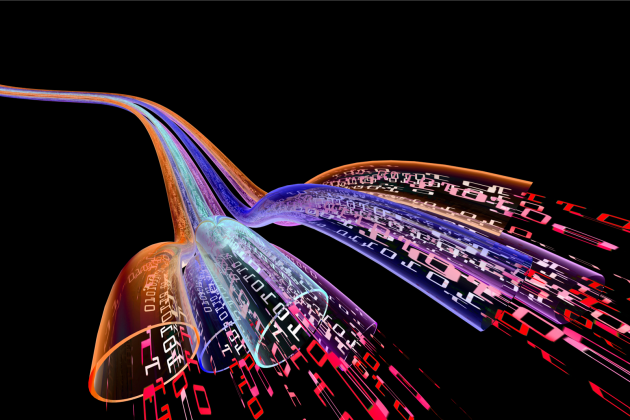
AI is in fact already taking on increasing significance in new projects. To maximise its benefits, it is important that it is matched to the right type of application. This will ensure that AI can contribute to solving a specific problem or meeting a particular requirement, with a clear economic advantage such as an increase in sales or margins.
One example where AI is now being used very effectively is for the grading of meat carcasses using cutting-edge image processing technology. This system can automatically determine the quality of the meat and decide the best utilisation of the carcass to deliver effective yield optimisation; or establish its optimal further processing into finished products.
Looking even further ahead, pick by voice and pick by vision as well as other BMI technologies could be joined by the introduction of “brain interfaces”. Using electroencephalography and holographic displays, operators can control production machines through their thoughts.
Combining all this in a smart way will ultimately take the resilience of the food industry to an even higher level.
For further case studies from CSB-System, visit the website, YouTube or LinkedIn.