Hygienic design is a term used freely in the manufacturing sector. HACCP International technical director Martin Stone explains why he prefers a more holistic definition with key criteria and considerations. This article first appeared in the October 2021 issue of Food and Drink Business.
My role with HACCP International involves the review of equipment specifically developed for use within the food industry. Much of this equipment is produced by some of the world’s leading manufacturers and I often hear the term ‘hygienic design’ tossed around. So, what exactly does it mean and why do we want it?
In its most basic form, hygienic design means easy to clean. But I like to consider a more holistic meaning where it means that all food safety hazards (including chemical, physical and microbiological) have been engineered to an acceptable level of likelihood occurrence, when used as designed (and sometimes when not).
Let’s have a look at some of the key criteria associated with hygienic design applied to a unit of equipment and what considerations should be undertaken when assessing hygienic design.
Surface matter
Surfaces should be considered in terms of being food contact or non-contact and there is an obvious gradient of risk in these cases. The material itself needs to be durable and impervious to food and liquid solutions.
Any coatings on the material such as plating or paints should be scrutinised carefully, as these elements are known to wear and/or chip off into the food stream.
When considering coatings, ask where a chip of that coating would end up if it was dislodged during operation or cleaning. The surface should not provide for any compound migration into the food and must be resistant to both the food and chemicals used to clean the surface.
At temperature extremes that can occur through washing or other uses, the materials may behave differently, and risks may increase.
Surface roughness is often considered, particularly for food contact surfaces, and is an indicator of how easy it is to clean. Quantitative measurements such as Ra are often used to describe roughness of a surface and should be considered based on intended usage of the surface. Ra is typically measured in microns (one millionth of a metre) and represents the average rise or fall of troughs and peaks from a mean line. That means, the average distance between a trough and a peak of a material with a Ra of 0.5 micron is one micron. The significance of this can be realised when seeing that a single bacterium is around one micron wide. Consequently, the Ra recommendation for food contact surfaces is typically below 0.8 microns.
Dead ends & hollows
Of course, roughness of a surface is only one aspect of how easy it is to clean the equipment effectively. Things like access to all parts of the equipment is important and where access is not entirely possible, the ability for the equipment to be easily disassembled (without specialised tools) becomes critical.
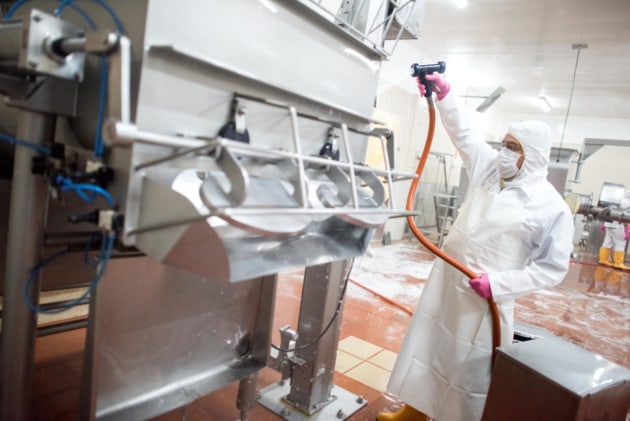
Further, there are design flaws that can make effective cleaning difficult or even impossible. Dead ends, hollows, poor quality welds and crevices are criteria to avoid completely as they can harbour food residue and microbial growth. They can also provide a platform for the development of biofilms, further complicating sanitation efforts.
Internal corners should not be sharp and should have a minimum smoothly curving radius of 5mm. As a rule of thumb, any gap, crevice, or depression not wider than 20mm cannot be easily cleaned. Where seals are used, these must be correctly sized to be flush with the adjoining surface, not too large forming a ridge or being recessed, thus forming a valley.
The nuts & bolts
Beware of equipment that features threaded fixtures like bolts and screws. Apart from potentially working loose and becoming contaminants, these fixtures are difficult to clean. Ideally, they should be absent from any food contact or splash zone. Round or dome head bolts onto compressible seals are best followed by external hex or square drive. If an internal head drive is absolutely necessary, then a fully slotted drive is the next best option. Internal drives such as Posidrives, hex drives, Torx or Phillips should be avoided at all costs in locations where cleaning is required.
In terms of more general considerations, there are several factors that warrant assessment. Consider parts of machinery that can fall out, wear or otherwise accidentally enter the product stream. If such risks exist, they can be mitigated if the potential contaminant is magnetic, metal detectable, or X-ray visible.
All equipment that is not able to be disassembled for cleaning needs to be self-draining such that small pools of wash water are not able to collect within the pipework or equipment.
Running hot or cold
Pay attention also to what happens with the equipment in use and when subjected to higher temperatures or lower than normal temperatures. At temperature extremes that can occur through washing or other uses, the materials may behave differently, and risks may increase. An example of this are conveyor belts situated at the end of a freezing tunnel where normal operating temperatures may well fall below zero leading to brittleness and breakages in some belting compounds.
And finally, consequence of error needs to be evaluated. What happens when the unexpected or an error occurs? Is the equipment failsafe? This is a really important part of hygienic design criteria which often is passed over in an assessment.
Fail & then rise
All of the above elements are reviewed when HACCP International conducts a certification assessment on a piece of equipment intended for use in the food industry. I can assure you, that many items submitted on the first occasion fail to meet our strict assessment criteria in terms of hygienic design.
Finally, one can take the principles of hygienic design on an individual piece of equipment and apply those same principles in the macro environment to the entire plant… Once you achieve that, you are really on the way to having a food facility that is fully compliant with the principles of hygienic design.
Martin Stone is a director of HACCP International, a leading Product Certification Body specialising in food safety risk management applied to the food and related industries. He has been associated with the food and food science sectors for 40 years.